Alimak is widely recognized as a global leader of industrial elevators built for the demanding requirements of various challenging industrial environments, such as those posed by tough marine conditions.
The remote and challenging environments involved in offshore wind power, rely on purpose-built Service Operation Vessels (SOVs) and Construction Support Vessels (CSOVs) for a range of essential duties, including transportation of wind turbine technicians and a variety of tasks involved in commissioning and the continuing operation of offshore wind farms. New SOV and CSOV vessels are currently under construction, and each of them will be equipped with a walk-to-work gangway, including integrated passenger elevator. Alimak have been successful and awarded several of these elevator contracts.
Marine elevators are exposed to extreme weather conditions, making the use of the most hard-wearing materials a key consideration. The challenge in this project was meeting the requirement for an elevator capable of achieving a variable travel height. This was addressed using a telescopic shaft that effectively adjusts the height of the entire elevator tower.
This system allows the lifting height to be increased to meet the needs of the largest wind turbine, or to be decreased in applications where height clearance would otherwise be an issue. Alimak developed a custom solution for this purpose based on a system with two sets of guide rails that the elevator car can run on, depending on the lifting height required.
Among other key factors were the size of the elevator shaft and car floor area. The Alimak solution benefits from a positive drive system, which does not require an additional travelling counterweight. The winch also allows for precise control of the stopping distance and minimizes the number of components involved, to simplify maintenance and maximum reliability.
This flexible vertical access solution will serve two distinct purposes, where separate elevators would otherwise be required. It will deliver access to the gangway bridge when required and operate as a standard elevator for transport between vessel decks. The dual functionality saves space, which is always a key consideration for marine vessels, and increases ride comfort for crew members.
ELEVATOR DETAILS
Application type: Service Operation Vessels
Elevator type: Traction, custom designed marine
Elevator model: ALIMAK ME
No. of elevators: 4 provided
Capacity: 2,000 kg
Elevator car size: 1.5 m x 2.9 m x 2.3 m (W x L x H)
Speed: 0.6 m/s
Lifting height: 24 m and 18 + 8 m (Telescopic)
No. of landings: 4 + 1 (Variable) and 3 + 1 (Variable)
First Alimak elevator on offshore support vessel with motion compensated gangway
Alimak has supplied an elevator for the pedestal of a new motion compensated walk-towork system on a new offshore support vessel named Vos Start. The Alimak elevator guarantees reliable transfer for the teams and their material between the vessel and wind turbines.
The Alimak rack and pinion elevator is used to provide easy and fast access for workers and goods from the new offshore support vessel’s main deck, warehouse deck and a motion compensated gangway. The gangway leads workers between the vessel and wind turbines or offshore platforms for service and maintenance work. The new vessel Vos Start has recently been mobilised with the latest motion compensated walk-to-work technology in Amsterdam’s ship repair Damen. It is a subsea-support vessel, purpose built to support offshore operations in the renewable industry and walk-to-work projects in the oil and gas industry.
The gangway system incorporates an access tower in which the Alimak elevator is installed, providing step less access. The adjustable pedestal provides full flexibility in landing heights.
The gangway system including the Alimak elevator has been provided by Barge Master and Bosch Rexroth — a unique system that enables reliable and efficient transfer of personnel and cargo no matter how tough weather conditions are.
CASE STUDY
No matter how tough weather conditions are, the Alimak elevator ensures reliable transportation of personnel and materials, between the vessel and wind turbines.
PROJECT CHALLENGES
Given the normal requirements of an offshore vessel such as the high roll and pitch motions and offshore demands, Alimak had three major project challenges: first, the elevator’s top landing needed to be variable; second, the amount of space available in the shaft was limited; and third, the timeline to complete the installation, testing and commissioning on the vessel itself was tight. Alimak strategically came up with the technical solutions to handle all challenging requirements with ease.
The elevator top landing is variable depending on the height of the windmill or offshore platform that is being serviced, thus stopping the elevator car at the exact same level as the motion compensated gangway.
The vessel was handed over to the end user in August, 2017 for its first job with offshore logistics support, accommodation and walk-to-work services provided during construction of an offshore wind farm in the Irish Sea
The operation of an Alimak rack and pinion elevator is not affected by rolls, pitches or heaves and the design is well suited for marine environments. These benefits and the narrow installation profile makes the Alimak marine elevator suitable for these conditions. Designed for the toughest environments on the planet, Alimak marine elevators have an expected life of 30 years at minimum with regular maintenance.
ELEVATOR DETAILS
Location: Offshore support vessel
Application: Motion compensated gangway
Elevator type: ALIMAK SE 2000 FC
Capacity: 2,000 kg
Elevator size (W x L x H): 1.3 m 2.2 m 2.1 m
Speed: 0.6 m/s
Lifting height: ~20 m (variable)
GALLERY
Alimak™ has showcased its engineering excellence with the installation of a second industrial elevator on the Svanen crane ship, enhancing its capabilities. This addition accommodates the vessel’s 25-metre extension, increasing its height from 80 to 105 metres. Known as the world’s largest crane vessel with a lifting capacity of 5,705 tonnes, the Svanen now benefits from improved operational efficiency, safety, and accessibility in demanding offshore environments.
Initially used as a crane for bridge construction projects, the Svanen has been widely utilised as a vital part of the construction infrastructure for around 650 offshore foundations. This includes the vast majority of monopole installations driven into the seabed of the key Baltic Sea region.
Alimak were initially selected as the ideal provider for a high functioning industrial elevator on board the Svanen based on our strong history of experience and expertise in the offshore industry, particularly in marine elevator and explosion proof elevator projects. We were also able to offer the client peace of mind and confidence in our ability to develop a practical industrial elevator solution for this specific purpose while remaining flexible on the location in order to avoid extensive modifications to this valuable ship. One potential location would have made for a more costly solution due to a surrounding angled structure. Through detailed forward thinking, assessment and planning processes, however, the Alimak team was able to site the industrial elevator in an optimum location while avoiding interference with essential cabling.
A further challenge in this kind of marine elevator vertical access system is the immense forces offshore vessels must deal with during construction work and in everyday operations. The crane itself is used to drive the base of the wind turbines deep into the ocean floor. The elevator developed for the particular needs of this project therefore uses special bolts and mounting methods to avoid the risk of them working loose under this extreme force and the safety hazard of a bolt dropping for up to 70 meters. The environmental forces faced by industrial offshore crane vessels such as the Svanen also present a number of specific vertical access challenges, particularly the high wind conditions.
This was further complicated by the high requirements for approval of elevators installed on Lloyds classified vessels. The optimum solution was to engineer an enclosure which allowed for the wind to flow through it on the first and second landing and decrease the stress caused by extreme weather conditions. The standard Lloyds regulations, however, did not cover approval for this particular approach. Alimak therefore carried out detailed risk assessments and worked closely with Lloyds to secure unit verification for this application.
In addition to the forces exerted by heavy machinery and environmental conditions, offshore vertical access solutions also commonly involve hazardous environments which require the enhanced safety of an explosion proof elevator. Alimak are recognised as a name to trust when it comes to safety in vertical access solutions for a broad range of high-risk industrial applications.
ELEVATOR DETAILS
Location: Travelling offshore vessel
Application type: Crane ship
Elevator model: ALIMAK™ SE 500
No. of elevators: 2
Payload capacity: 500 kg
Elevator car size: 1040 x 1170 x 2170 mm (W x L x H)
Speed: 0.4 m/s
Lifting height: 69 m and 25 m
No. of landings: 3
Installation years: 2020 and 2024
GALLERY
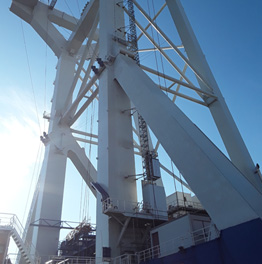
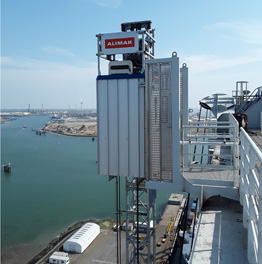
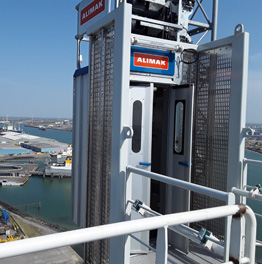
Four Alimak rack and pinion offshore elevators utilized as safe column access to various levels for men and materials onboard the semi-submersible production platform FPF1 (formely owned by Amarada Hess and known as AH001).
The Alimak OS-4 rack and pinion offshore elevators are a vital means of safe access to the columns for men and materials, so are essential during both operations and shipyard stopovers. The original elevators have been in successful service since 1976 (38 years) and the intention is that the newly refurbished elevator cars will supply uninterrupted access within the hull columns for many years to come. The elevator modernisations were part of a major modification and refurbishment of the FPF1 in the Remontowa Shipyard in Poland, prior to deployment to the Ithaca operated Stella field in the Central North Sea.
Elevator details
Location: Petrofac FPF1
Platform type: Semi-submersible production facility
Application: Hull column
Installation year: 1976
Refurbishment year: 2013
No. of Elevators: 4
Elevator type: Rack & Pinion
Elevator model: ALIMAK OS-4
Capacity: 1,000 kg
Elevator car size: 1.5 m 1.5 m 2.3 m (W x L x H)
Speed: 0.36 m/s
Lifting height: 18 m
GALLERY
Imagine living and working in an environment where temperatures can reach –50°C. A place where snowfall is so intensive that it has necessitated periodic rebuilding of snow-crushed buildings around every ten years. Welcome to the Halley Survey Base in Antarctica, year round home to a maximum population of researchers and scientists.
An unusual application for an Alimak goods elevator involves a unit that was supplied by Alimak to Structaply Limited, Ross-on-Wye, Herefordshire in 1983. Structaply manufacture insulated timber buildings was awarded a contract for a twin 2-storey articulated building to provide accommodation for 18 scientists at the Halley survey base in the Antarctic. Built directly onto the ice cap, the accommodation was designed for a life-span of 15 years, and in that time increasing snow falls that freeze, combined with the settling of the building itself, will submerge it to an estimated maximum depth of 20 meters below the surface (summer temperatures at the base average —30°C, winter temperature approximately —50°C).
Services Consultants, Dale & Goldfinger, insisted that the equipment was guaranteed to withstand temperatures to —50°C, and Alimak was able to so guarantee the equipment without the need for special steel certification. No other elevator manufacturer was prepared to bid for the contract with this stringent temperature requirement, and this highlights the high quality used in the standard Alimak product range.
The Alimak elevator had a maximum capacity of 1,150 kg and was erected to facilitate the movement of materials between the building and the variable surface during the building’s life until 1998. The unit supplied was a standard elevator from the range, although low temperature lubricating grease and space heaters for the cabinet/worm gear were supplied. The Alimak elevator was selected because of its complete reliability, and its ability to withstand the extreme cold. Maintenance engineers from Antarctic survey team were specially trained in the installation and maintenance of the equipment at the Rushden works of Alimak.
According to Structaply the accommodation building which is housed in 4 tubes and manufactured in double skin plywood can withstand an crushing pressure of 9 tons per square metre. The high standard of insulation necessary for the men’s survival and comfort will also prevent melted snow re-freezing beneath the building and causing damage to the underside of the structure — which has been a serious problem in previously used corrugated steel designed buildings.
ELEVATOR DETAILS
Location: Halley Survey Base, Brunt Ice Shelf, Antarctica
Installation year: 1983
Application: Research Station
Elevator type: Rack & Pinion
Elevator model: Alimak Scando M
Capacity: 1,150 kg
Lifting height: 20 m